Super Spacer® makes “glazing art” possible
Ranging from the “most complex building in the world”, the Museum of the Future in Dubai, to the spiral glass pavilion of the Audemars Piguet Museum in Le Brassus – Super Spacer® can lay claim to some very spectacular world premieres in facade technology in its list of references. The main reasons for this are the flexibility of the material during the production of free-form insulating glass and the high mechanical load-bearing capacity of structural glazing.
“Architecture is the canvas for the stories of our lives “, Bjarke Ingels once said. He is not only one of the most famous contemporary architects, but also a very gifted storyteller. And he feels the real task of his profession involves turning dreams into reality. Whether it’s with the aid of Lego bricks or the digital version of “Minecraft”, people wish to transform their fantasies into reality. In the real world, architecture is often, by its very nature, subject to limitations.
This is why prestigious objects such as museums as well as concert halls and art galleries are so coveted in the architectural scene, since clients rarely impose limits on their designs. “Spectacular cultural buildings are tourist attractions and can become modern landmarks,” says Joachim Stoss, Vice President International Sales at Edgetech Europe/Quanex. Via the curved insulating glass of the Berlin-based company Döring Glas, which has been operating as vandaglas since 2021, the flexible Super Spacer® is displayed in various museums; among other things, in sensational projects designed by the BIG Bjarke Ingels Group office such as the world’s first refugee museum FLUGT in Denmark and the art museum “The Twist” not far from Oslo.
The supreme discipline of glass bending: Three-dimensionally free-formed insulating glass
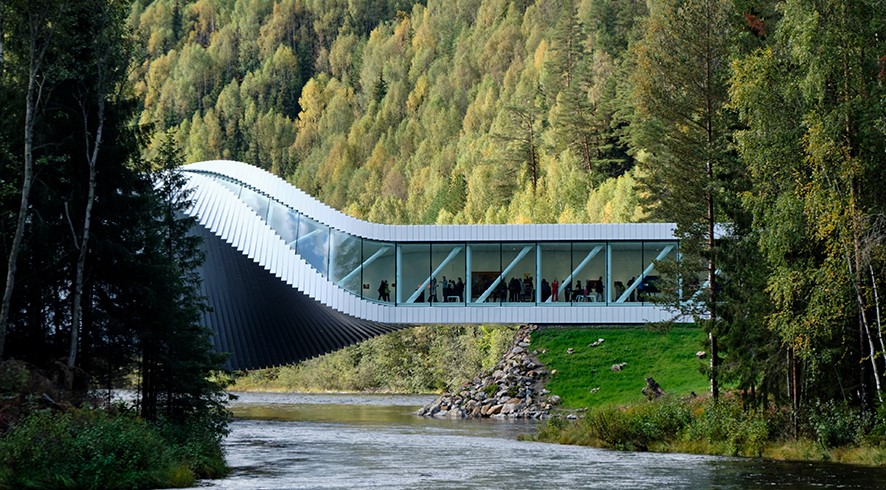
A short distance from Oslo, masterpieces by Yayoi Kusama, Fernando Botero or Olafur Eliasson await you on the grounds of the Kistefos Art Museum in the middle of the Norwegian forest landscape. “The Twist” closes the circular path through the sculpture park above the Randselva River. The spectacular 90-degree rotation transforms the gallery itself into a sculpture.
Döring supplied ten quadruple-glazed insulating glass elements with a glass package that is 55.04 mm thick for the structural glazing facade. The free-form units are manufactured using SSG Climaplus Contour with Super Spacer® TriSeal™. A PVB film blocks the UV radiation to shield the artwork from sunlight. The IGS elements cover a total area of 98 square metres, the largest element covers an area of 5.2 × 2.5 metres and weighs an incredible 1.2 tonnes.
One of the largest floating art installations in the world, the “Salmon Eye”, which opened in Hardangerford in September 2022, is also located in Norway. Initiated by Eide Fjordbruk, the world’s first salmon producer to be certified for its CO2-neutral production, exhibitions and events covering an area of 1,000 square metres and extending across four floors are designed to inspire and inform us about the topic of the “improved supply of our planet with sustainable seafood”.
The Salmon Eye
One of the largest floating art installations in the world, the “Salmon Eye”, which opened in Hardangerford in September 2022, is also located in Norway. Initiated by Eide Fjordbruk, the world’s first salmon producer to be certified for its CO2-neutral production, exhibitions and events covering an area of 1,000 square metres and extending across four floors are designed to inspire and inform us about the topic of the “improved supply of our planet with sustainable seafood”.
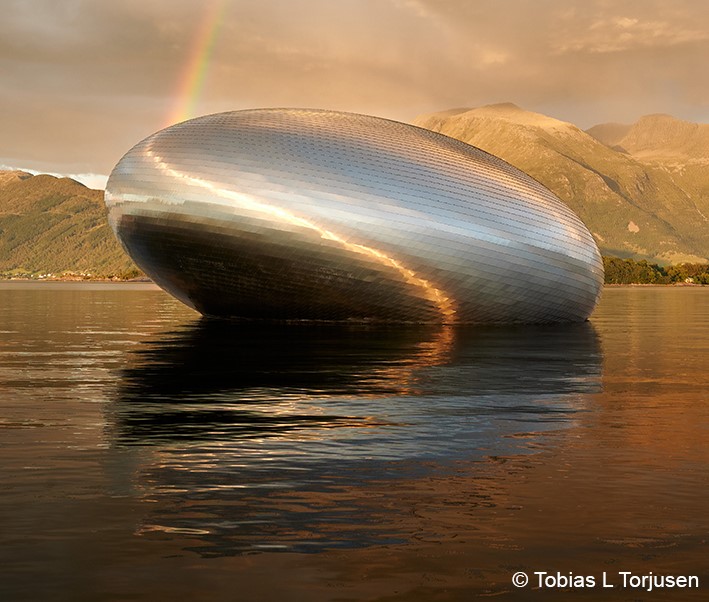
The double-curved, ellipsoidal shape is modelled on a salmon’s eye, the outer skin made of 9,250 stainless steel plates imitates the shimmering silvery fish skin. Despite its weight of 1,256 tonnes, the floating pavilion designed by Kvorning Design has an elegant and light appearance. vandaglas supplied seven curved double-glazed insulating glass elements for the exterior panes. These result in a total arch length of around 16.6 metres. The laminated safety glass “CurvePerformProtect” with Super Spacer® TriSeal™ Flex, a spacer specially developed for curved glass, was used. As with the Kistefos facade, the panes are shaped three-dimensionally.
The number of glass benders actually capable of producing such insulating glazing in Europe is small. Carsten Kunert, vandaglas’ Sales Manager, describes the challenges: “The difficulty with parametric 3D freeforms is to break down the 3D file from the BIM modelling to the neutral chamfer of the glass. Before actually bending it, the dimensions of the individual glass blanks must be determined for each individual bending plane, while taking into account the glass structure. Moreover, we require individual steel bending moulds for these multi-axis bends for each glass, which support the glass packages that weigh several tonnes at temperatures of up to 650 °C throughout the entire process. It was only through the use of state-of-the-art 3D drawing programs, direct data transfer to precision machines for mould making in addition to digital 3D measuring instruments that such complex shapes became possible in the glass construction sector. But despite highly intelligent simulation tools, the physical behaviour of the glass cannot always be precisely calculated. Spherical freeforms often require the use of trial-and-error bending tests as well as a large amount of experience.”
Facade technology at the outer edges of what is possible
The Musée Atelier Audemars Piguet in Brassus, a small town more than 1,000 metres above sea level in the Swiss Jura Mountains, aims to tell “the story of talented watchmakers who, for generations, have continually pushed the boundaries of their craft”. A glass double helix, that nestles in the landscape like a giant watch spring and is connected to the historic building where Audemars Piguet was founded in 1875, forms the heart of the new museum. Viewed from the outside, the curved all-glass facade, the 470-tonne greened steel roof, and the striking sunshade louvre fashioned from untreated brass determine its appearance. The pavilion takes the concept of structural glazing to the technological extreme in an unprecedented manner. In the absence of additional supports or stiffeners, the 101 curved, trapezoidal elements of the glass facade bear the loads. To achieve this, the insulating glass units are bonded at the top and bottom in specially manufactured steel shoes using a high-modulus silicone sealant. Injection mortar prevents the glass edge and steel from touching.
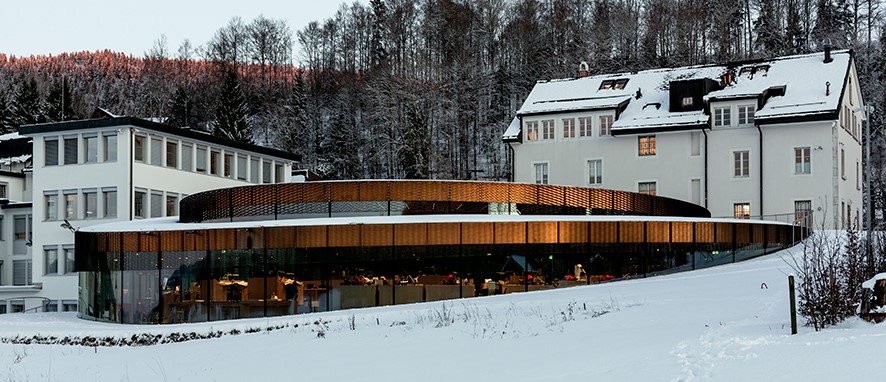
The realisation of this vision was preceded by an intensive, technologically challenging collaboration between the BIG design team, the structural engineers from Lüchinger+Meyer Bauingenieure, the facade specialists FRENER + REIFER and the glass manufacturer SFL Glastechnik as the main protagonists, as well as countless load tests – involving loads of up to a maximum of 80 tonnes – and ageing tests.
In view of the harsh microclimate in the Vallée de Joux, snow loads of more than 5 kN/m2 and minimum temperatures of well below minus 20 °C had to be taken into account in the construction. In addition, the facade had to meet the Swiss Minergie standard for energy efficiency. The triple glazed insulating glass was produced to achieve a Ug value of 0.5 W/(m²K).
The sizes of the insulating glass units range from 2.4 m x 1.5 m to 2.4 m x 5.5 m. Although only four different bending radii were required, each unit is unique due to the fact that the top and bottom edges followed the natural course of the terrain.
The thickness of the laminated glass structure of the interior walls increases from the outside to the centre of the spiral up to 66 mm, consisting of up to 5 x 12 mm layers plus SGP film. The glass packages of the exterior facade are each 96.5 mm thick. The inner, load-bearing pane consists of triple laminated 12 mm solar control glass SunGuard® SNX 60/28 float glass with a SGP film, the middle 8 mm pane is unlaminated and the outer pane is 2x 8 mm laminated glass. SFL Glastechnik chose the Super Spacer® TriSeal Flex in black as the spacer.
“While it’s true that thick glass packages only slowly heat up in the summer, it is intensive nevertheless. The partial shading of the glass by trees and other obstacles can lead to high temperature differences in the glass and thus to different degrees of expansion,” explains Christoph Rubel, European Technical Manager at Edgetech, and continues: “Due the fact the thick glass structure is very stiff, the edge sealant must absorb any change in pressure in the space between the panes using spacers and silicone sealant.” What’s more, curved glass is in itself stiffer than flat glass and thus even higher climatic loads act on the edge seal in the space between the panes. Joachim Stoss explains the key advantage of the main material of a Super Spacer®: “The structural foam made of silicone is flexible, offers 100 percent resilience and can absorb even the highest mechanical loads. This ensures the tightness of the edge seal, which is of course a necessary property of every IGU. But due to the enormous value of the glasses made for this project it was especially important to prevent moisture from penetrating into the space between the glass panes and impairing their transparency.”
Whether in the Swiss mountains, in Norway’s arctic climate, or in a hot desert climate, the edge seal of structural insulating glass units must withstand all mechanical forces caused by temperature changes, wind and gravity without exception. The fact that Super Spacer TriSeal™ withstand even the greatest loads without any problems has been proven in a hurricane simulator at a wind speed of 350 kilometres per hour subject to positive pressure and at a wind speed of 395 kilometres per hour under suction. Christoph Rubel explains: “Rigid spacers form a sharp edge in the edge seal when a certain pressure load has been exceeded, at which the glass can break. A flexible spacer also makes the edge seal flexible and dramatically reduces the risk of breakage here.”